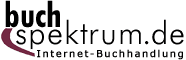 Neuerscheinungen 2015Stand: 2020-02-01 |
Schnellsuche
ISBN/Stichwort/Autor
|
Herderstraße 10 10625 Berlin Tel.: 030 315 714 16 Fax 030 315 714 14 info@buchspektrum.de |
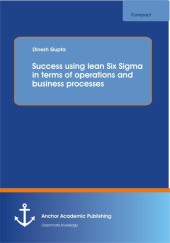
Dinesh Gupta
Success using lean Six Sigma in terms of operations and business processes
Erstauflage. 2015. 32 S. 220 mm
Verlag/Jahr: ANCHOR ACADEMIC PUBLISHING 2015
ISBN: 3-9548934-1-X (395489341X)
Neue ISBN: 978-3-9548934-1-6 (9783954893416)
Preis und Lieferzeit: Bitte klicken
Lately thereīs been a great deal of talk around Lean execution. But, some people speak of Lean, some speak of Six Sigma and some use a combination of the two. But, whatīs the difference? How do you know whatīs right for your organization? As the market place tightens and companies are fighting for every dollar of revenue, they need to adopt innovative methods to create more efficient processes that will give them a competitive edge of their closest rivals; this is the basis for Lean Six Sigma. Unlike traditional Six Sigma, Lean Six Sigma uses some of the methodology from lean manufacturing along with the Six Sigma approach. Many organizations see Lean Six Sigma as the evolution of the Six Sigma methodology rather than a modification. Lean Six Sigma takes the fundamentals of Six Sigma and incorporates the cost reduction principles of Lean Manufacturing.
Text Sample:
3.3.1 DMAIC
Basic methodology consists of the following five steps: Define the process improvement goal or problem to be solved this should be consistent with customer requirements and the business strategy. Measure the current process and collect relevant data for future comparison. Analyse to verify relationship between factors and to identify the real root causes ensuring that all factors have been reviewed. Improve or optimize the process based upon various analysis tools to identify a number of solutions and then using data determine the most optimum for the problem
Control to ensure that the solutions is implemented into the organisation and embedded so that it is does not return. This uses a series of tools and techniques to continuously measure the process and institute control mechanisms. Basic methodology consists of the following five steps: Define the goals of the design activity that are consistent with customer requirements and business strategy. Measure and identify CTQs (critical to qualities), product capabilities, production process capability, and risk assessments. Analyse to develop and design alternatives, create high-level design and evaluate design capability to select the best design. Design details, optimize the design, and plan for design verification. Verify the design, set up pilot runs, implement production process and handover to process owners.
Many people get confused by Six Sigma and believe that it is simply a case of applying a number of tools. This has lead to many failed implantations of the methodologies. Other are put off Six Sigma by the amount of data collection and analysis which is used. Simply put Six Sigma is all about data, if you have not got data you are just another person with an opinion. One of the reasons Six Sigma has been so successful in companies such as Motorola is that it is all data driven the methodology makes you use the data, analyse the data and then come up with solutions. To do this you must use statistics and tools which use stats to investigate and solve problems. As such typical tools used in Six-Sigma include:- Regression analysis, design of experiments and Chi-square testing may be used to define/identify within each sub-process, the possibilities for defects or quality problems.Statistical tools as well as conventional quality techniques like Brainstorming, Root cause Analysis, Fishbone Diagram, Pareto analysis etc may be used for carrying out analysis.While implementing process controls in the final stage of six sigma implementation the POKA-YOKE (mistake-proof) devices can be set up to obviate the inadvertent errors to hold the gain that have been obtained from the improve stage.The idea POKA-YOKE is to respect the intelligence of workers by taking over repetitive tasks that depend on vigilance or memory.
They can seem daunting and put off many people but the simple truth is that you donīt have to know them all. You donīt even need to use them all. It is good ideas to have one or two people in your organisation who have detailed knowledge of them all you have to do is to know when they should be used then call in the experts.
When used properly Six Sigma can dramatically reduce variation in your processes and lead to massive savings. However when coupled with Lean it becomes even more powerful.
Lean as the name suggest is the production of products or services using the least of everything - human effort, investment in inventory, machines, space, tools, time, development, transport / movement. The term is called Lean, Lean Manufacturing and Lean Enterprise all meaning the same thing and deriving from the Toyota Production system and some other sources. It is however very simply the reduction of waste from your processes it has enabled Toyota to become one of the biggest and most reliable car companies in the world.
Lean is therefore the identification and steady elimination of waste through the implementation of perfect f